
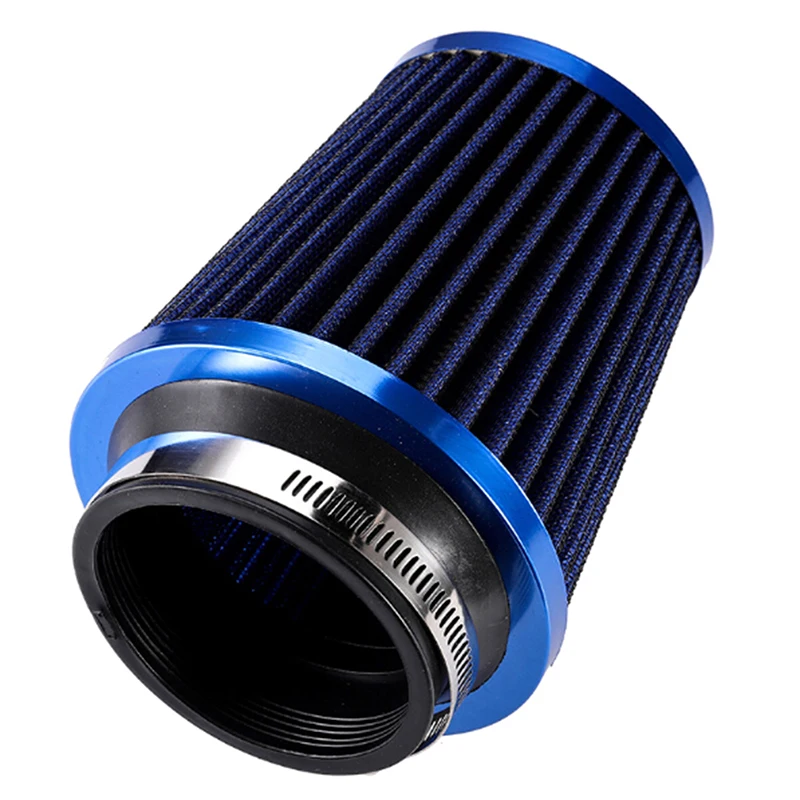
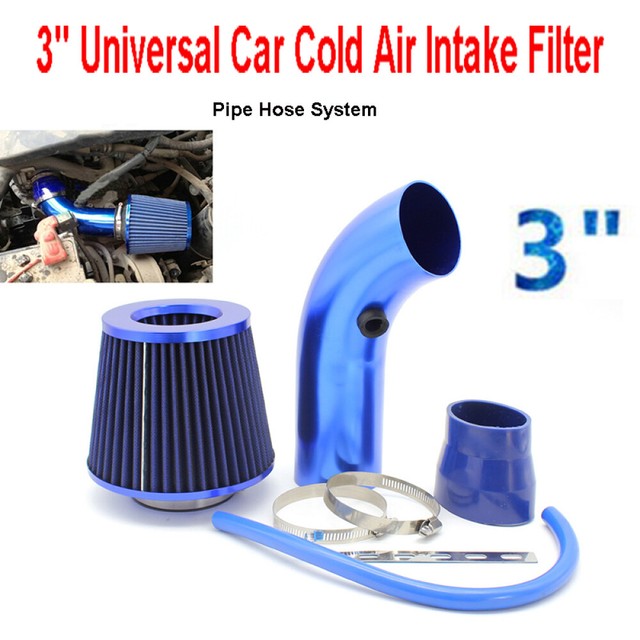
14.16(a), consequently the area heavily subjected to vortex swirl and negative pressure will be at a minimum. If the body was shaped in the form of a tear drop, the contour of the body would permit a boundary layer to continue a considerable way towards the tail before flow separation occurs, see Fig. If the streamline contour of the body is such that the boundary layers cling to a converging rear end, then the vortex area is considerably reduced with a corresponding reduction in rear end suction and the resistance to motion. 14.16(a and b)) The shape of the car body largely influences the pressure drag. With these contours the drag coefficient can be as low as 0.05.ġ4.2.6 Base drag (Fig. Thus the resistance to body movement will be mainly due to viscous air flow and little to do with vortex wake suc tion. 14.15(f)) If the proportion of length to diameter is well chosen, for example 0.25, the streamline shape can maintain a boundary layer before flow separation occurs almost to the end of its tail. For some unknown reason (possibly due to the very gradual alignment of surface curvature with the direction of air movement near the rim) the hemisphere provides a lower drag coefficient than the cone and the sphere shapes this, being of the order of 0.42. The curvature of the hemisphere gradually aligns with the main direction of flow after which flow separation takes place on the periphery. 14.15(e)) Air flow towards and outwards from the centre of the hemisphere. There is therefore a slight reduction in the vortex wake and similarly a marginal decrease in the drag coefficient to 0.47 compared with the 60° cone. 14.15(d)) Air flow towards the sphere, it is then diverted so that it flows outwards from the centre around the diverging surface and over a small portion of the converging rear half before flow separation occurs. 14.15(a-e) Drag coefficient for various shaped solids This profile halves the drag coefficient to about 0.5 compared with the circular plate and the cube block. Flow separation however still takes place at the periphery thereby producing a wide vortex wake. 14.15(c)) With the piecing cone shape air flows towards the cone apex and then spreads outwards parallel to the shape of the cone surface. 14.15(b)) Air flow is head on but a boundary layer around the sides delays the flow separation nevertheless there is still a large vortex wake and a high drag coefficient of 1.05. Flow separation takes place at the rim this provides a large vortex wake and a correspondingly high drag coefficient of 1.15.

14.15(a)) Air flow is head on, and there is an immediate end on pressure difference. A comparison of the air flow resistance for different shapes in terms of drag coefficients is presented as follows:
